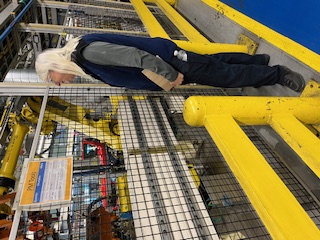
Manufacturing Execution Systems
MITS: Tailored Solutions for Your Manufacturing Execution System
Manufacturing IT Solutions (MITS) is a versatile Manufacturing Execution System (MES) designed to monitor and document the real-time transformation of raw materials into finished products within facilities.
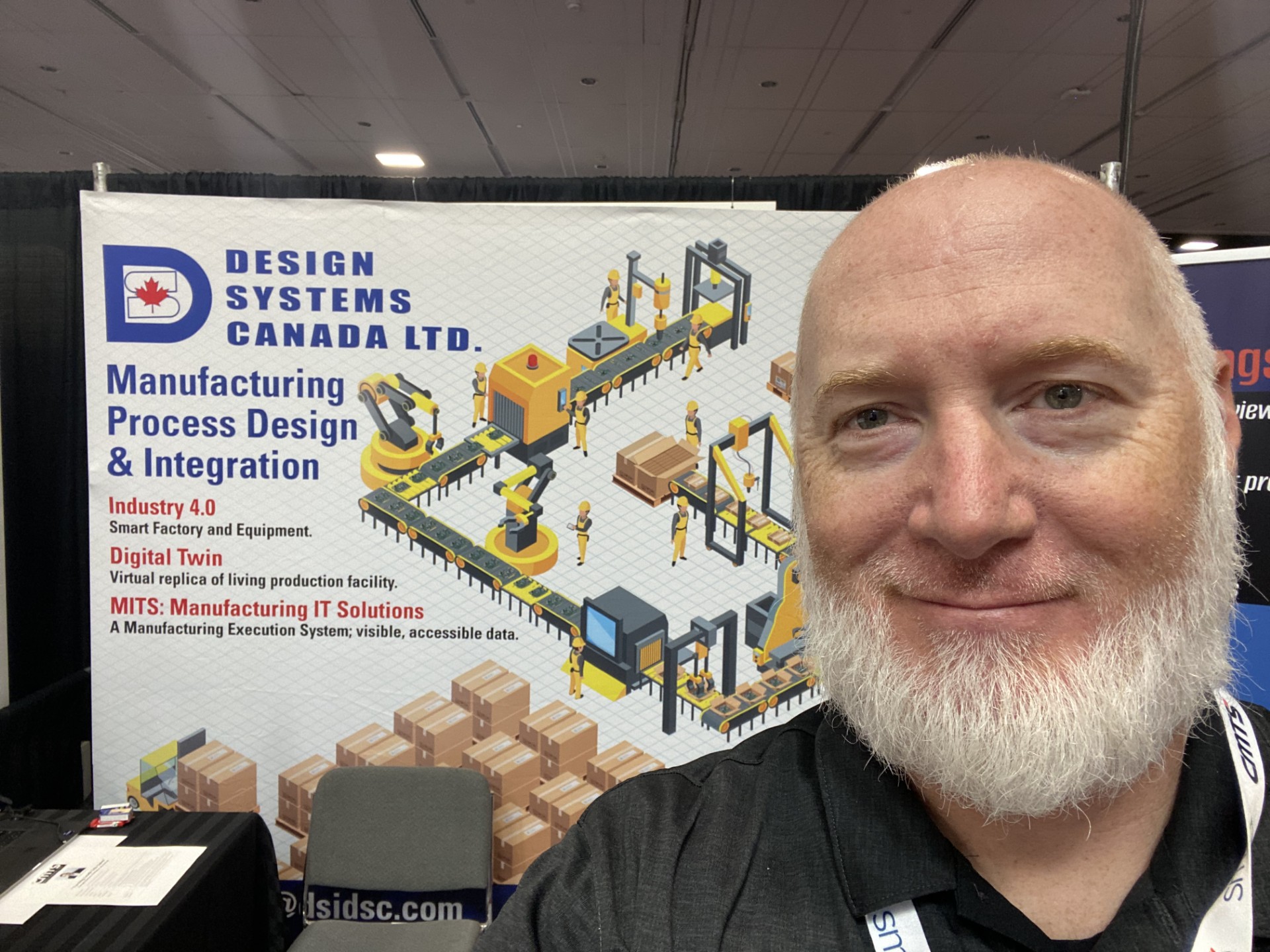
Overview of MITS Manufacturing Execution System
Production Monitoring: Gain instant visibility into your production facility, accessible at any time.
Order Management: Seamlessly manage orders from ERP systems, flat files, or scan-and-load processes, ensuring smooth tracking throughout the build cycle.
Lean Manufacturing Integration: Support for Lean Manufacturing tools, including VSM, Poka-Yoke, Pick-to-Light, Kanban, Pick-to-Voice, Andon, and more, tailored to your needs.
Tracking and Genealogy: Monitor and document every step, from raw materials to finished goods, with comprehensive product data tracking.
Maintenance Support: Enhance maintenance operations to minimize downtime and maximize efficiency.
Error Proofing: MITS equips you with tools to incorporate error-proofing mechanisms into existing processes seamlessly.
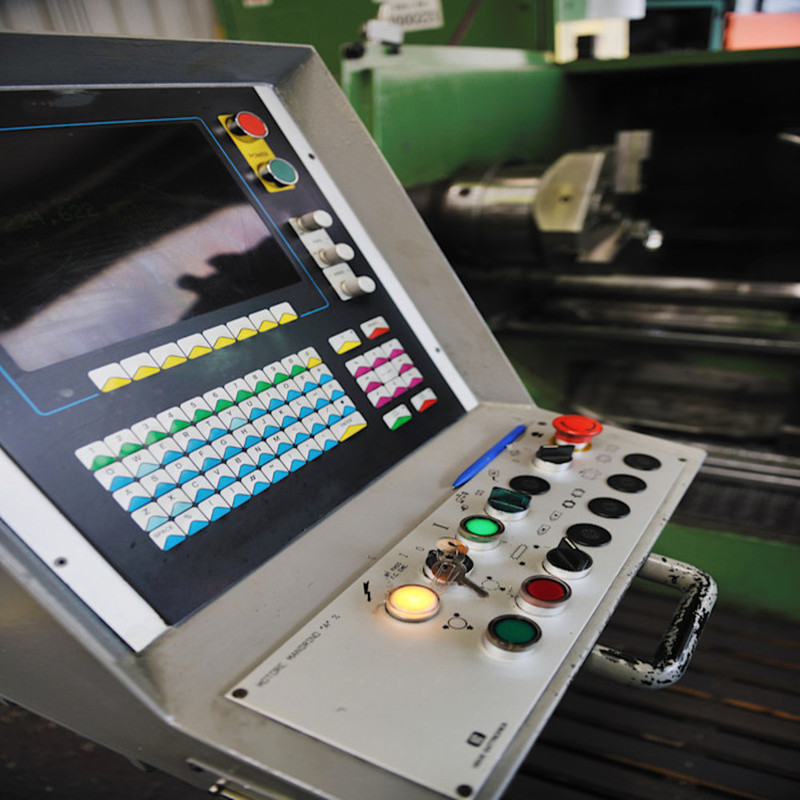
Deploying a Manufacturing Execution System (MES)
A Manufacturing Execution System (MES) carries out a variety of essential tasks, with its capabilities continually refined by international standards and models over time. Key examples include:
Performance Evaluation: Through an audit interface, MES integrates data from various systems to assess and optimize production performance.
Production Tracking and Tracing: MES provides a comprehensive history of equipment, lots, and orders by recording and retrieving related data, ensuring full traceability upon request.
Production Performance Analysis: Metrics such as overall equipment effectiveness (OEE) and real-time Work-In-Progress (WIP) overviews are analyzed to generate actionable insights for performance improvement.
Production Process Scheduling: MES integrates with systems like ERP to receive production requirements and optimizes local resources to create efficient production schedules based on work orders.
Resource Management: By analyzing, recording, and sharing information, MES ensures resources are properly allocated and prepared, supporting seamless execution of production orders.
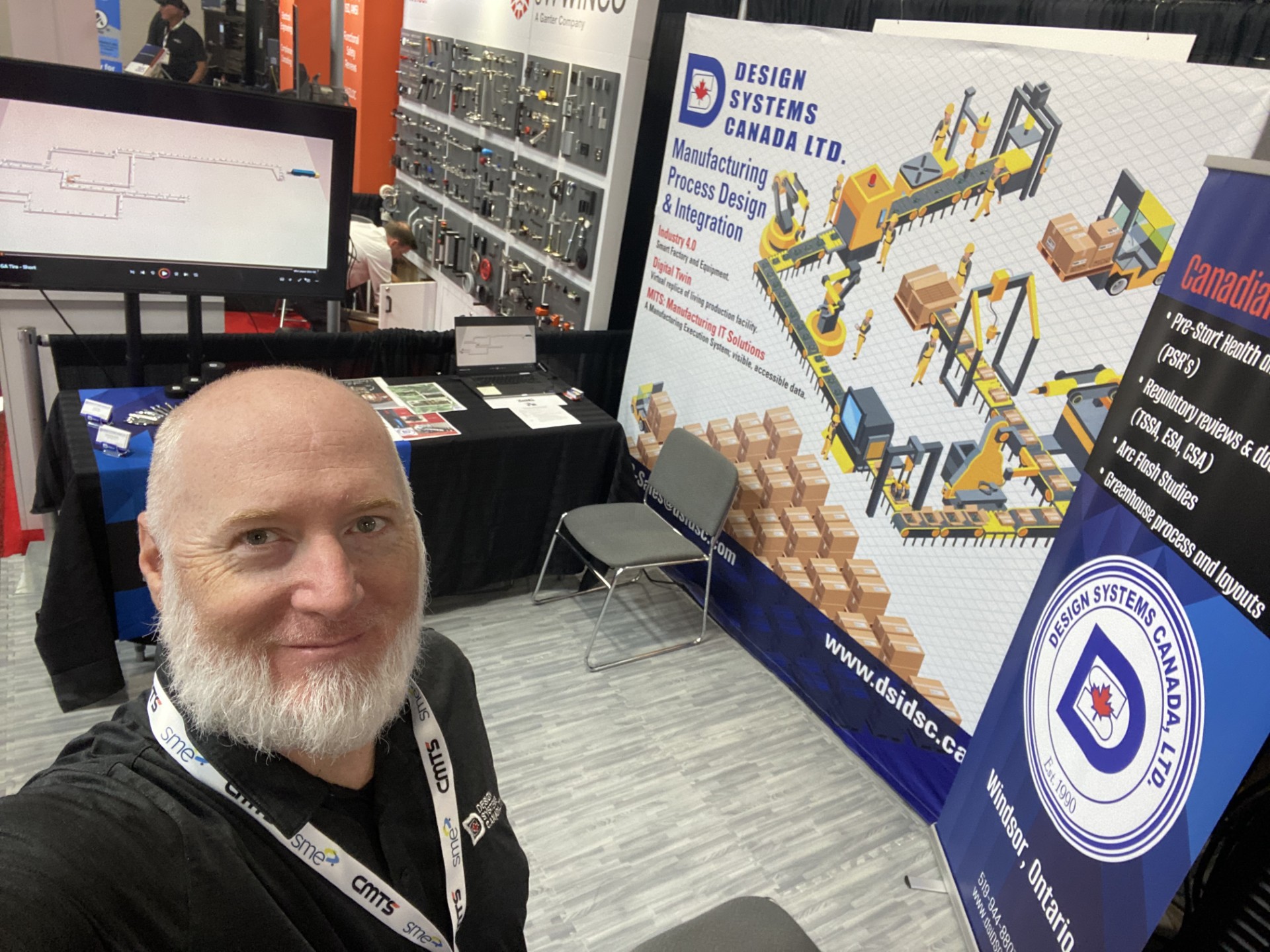
The Fourth Industrial Revolution
Advancements in data exchange, cloud computing, and automation have led to the emergence of "smart factories," a key concept of the fourth industrial revolution, also known as Industry 4.0. Smart factories focus on improving efficiency by leveraging manufacturing analytics to collect and analyze time-series data.
This analysis enables manufacturing decision-makers to optimize production output by enhancing current conditions on the factory floor.
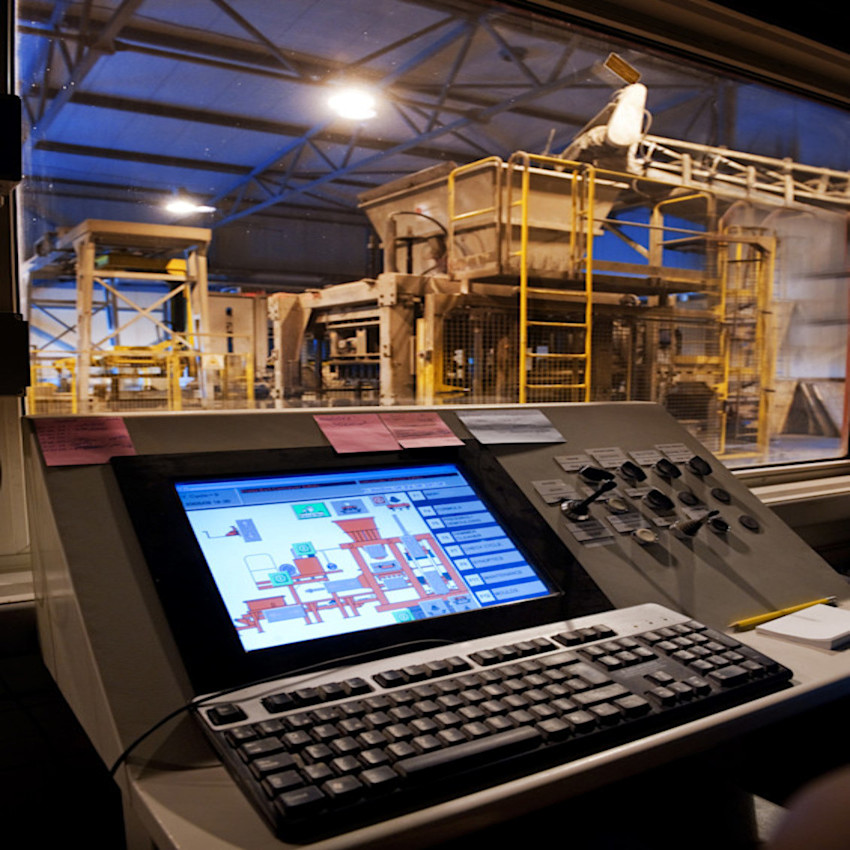
During the development of Industry 4.0 systems
Overlapping functionalities among various systems created a need for better structure. To address this, the Manufacturing Enterprise Solution Association defined the scope of MES with specific functions.
These functions focus on:
Machine Downtime
Plant Visibility
Throughput Challenges
Quality Concerns
Traceability Gaps
Process Visualization
Order Management
Assembly Operations
Logistics
Maintenance Support
Key Benefits of This Approach:
Waste Reduction
Increased Uptime and Throughput
Transition to Paperless Operations
Lower Inventory Levels
Improved First-Time Compliance Rates
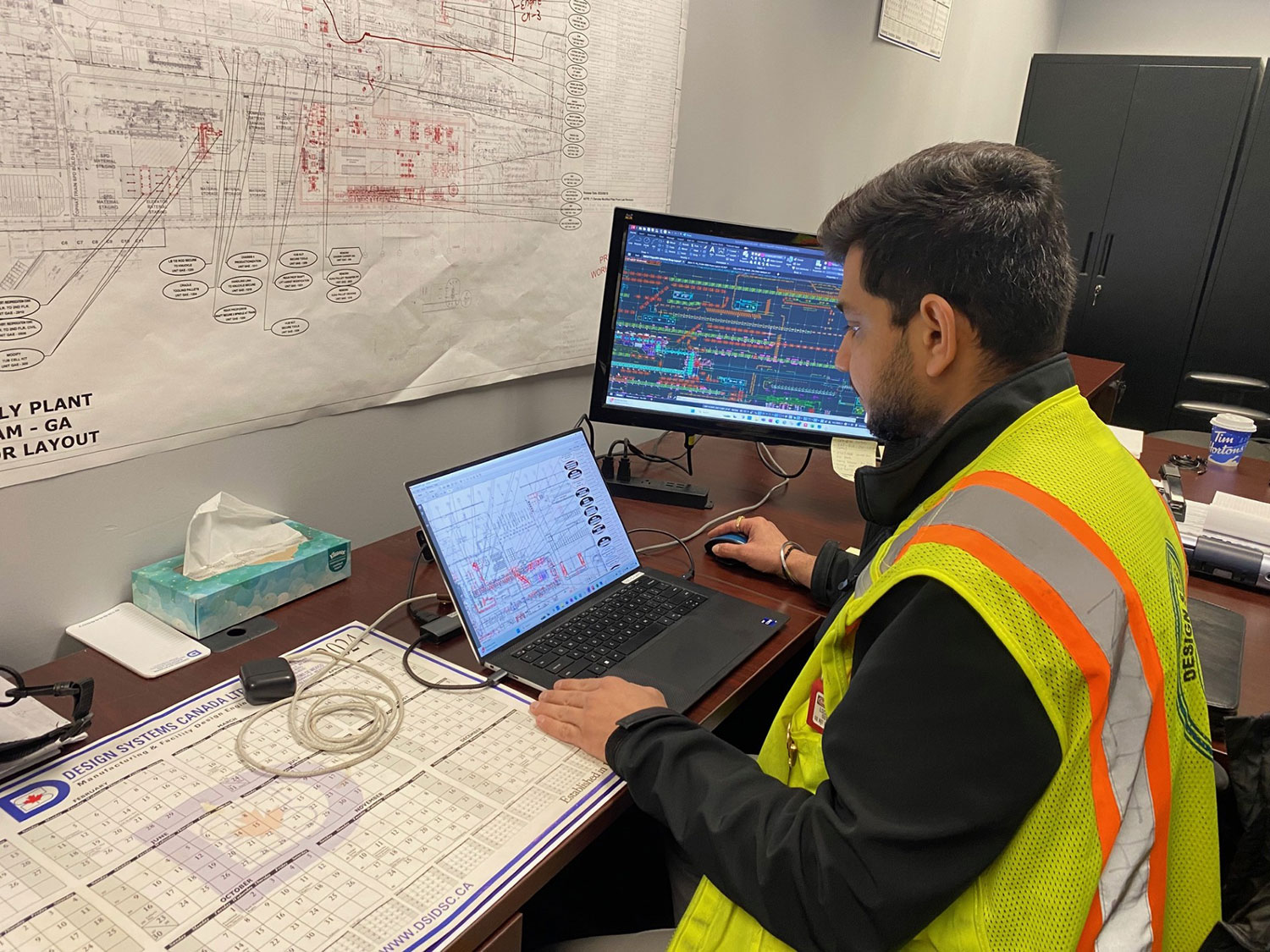
Why Design Systems Canada?
DSC is ready to guide clients through the journey of Industry 4.0 and the evolution of MES.
Whether you operate a small manufacturing facility or a large-scale enterprise, MES is a critical tool for achieving operational excellence. For tailored support in implementing MES within your operations, reach out to us today. MES enhances process efficiency, boosts quality, and drives data-informed decision-making.
Exploring the key components, advantages, and transformative potential of MES will demonstrate why it is an indispensable asset for modern manufacturing success.